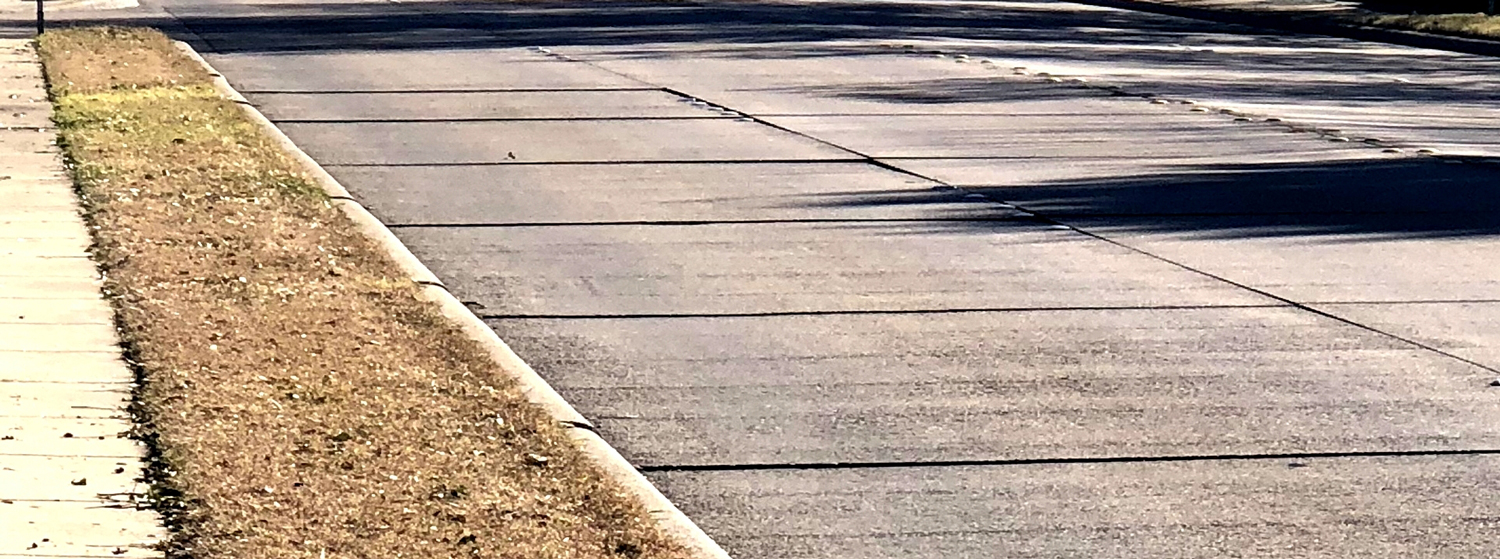
FAULTED PAVEMENTS
FAULTED CONCRETE PAVEMENT - POLYGRINDING
Poorly compacted foundation soils, water penetration, and increasing heavy tractor trailer loads are the main causes of faulted pavement. Nortex has pioneered a process we call “PolyGrinding” which not only provides a solution for the issues below the slabs, but also solves the problem on top of the slab by improving ride quality. The injection of high-density polyurethane combined with concrete joint grinding allows us to properly repair and strengthen the soils below, and grind down any offset joints above - all under the same lane closure. Many cities and transportation departments have found this process to be a quick, cost effective, and long lasting solution vs. full depth repair or dowel bar retrofit.
FAULTED PAVEMENT PROJECTS
TRANSVERSE JOINT FAULTING - POLYGRINDING
Faulting along the transverse joint (or expansion joint), is a very common problem among arterial city streets and state highways. This faulting causes a washboard effect, and can be felt and heard when driven over. Our high-density polyurethane foam injection process, combined with with grinding at the expansion joints, has proven to greatly improve the ride quality, and prevent future faulting. As the foam is injected, it first fills any voids created by water intrusion and/or settlement of sub-grade soils over time. The foam then begins to compact these soils, followed by vertical lift until the joint correctly realigns. Any joints that are not able to be matched perfectly will be ground down to provide a smooth ride. The compressive strength and hydrophobic nature of the foam allows for a long-lasting solution. Many cities and transportation departments have chosen this process because it works. Road deflection tests have proven that it greatly increases the ride quality index. Our crews are capable of fixing up to one half lane miles per day, preventing long periods of unwanted down-time and disruption.
Pictured directly below is a photo that depicts how polygrinding at the expansion joint greatly improves ride quality. In addition, there is a collection of photos from multiple projects that we have completed for city and state clients.
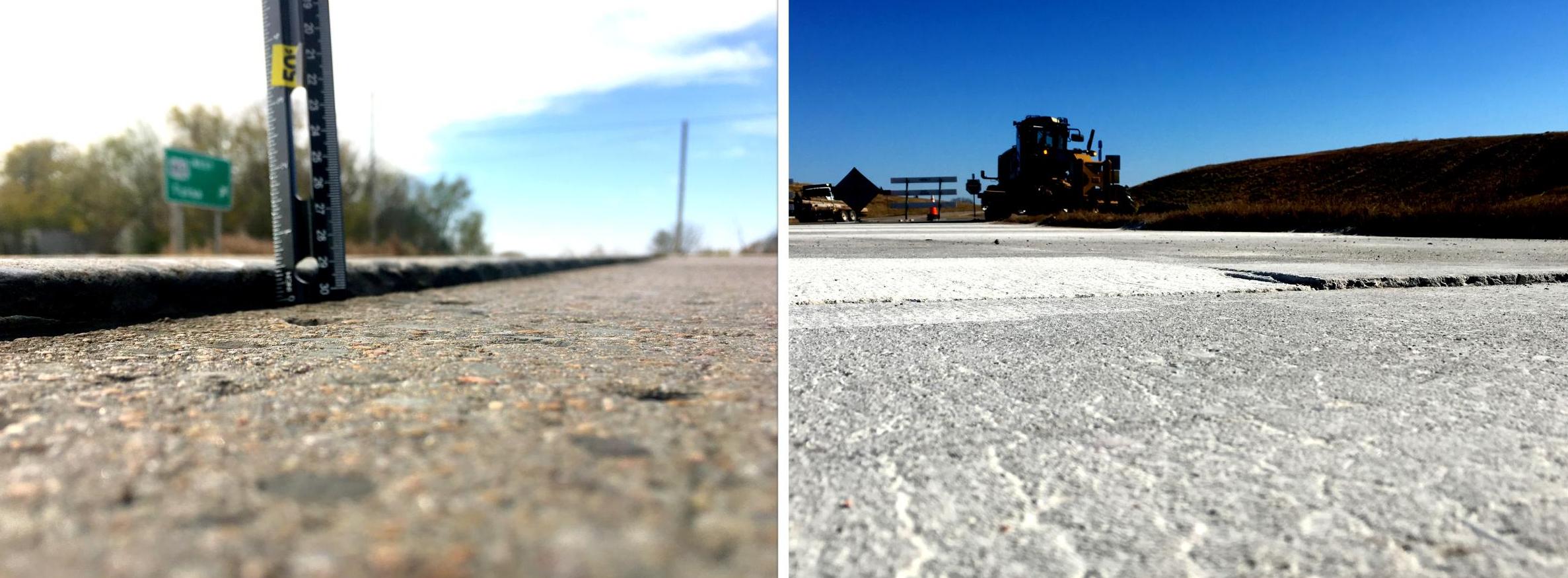
LONGITUDINAL JOINT FAULTING
Faulting along the longitudinal joint, in many cases, have the tendency to be more severe due to the lack of rebar between the joints of the concrete slab. Severe faulting, as pictured in each of the projects below, poses safety hazards for drivers- especially motorcyclists. Fortunately, the high-density polyurethane injection process is able to lift and match these joints with ease, eliminating the issue altogether. Our foam has a compressive strength that is strong enough to withstand the constant impact of heavy tractor-trailer loads. This prevents further slab settlement, extending the life of the pavement for years.
Each of the four projects pictured below were completed in one day or less. We provided our own traffic control, keeping at least one lane open for traffic at all times.
DRILLING IN ACTION
Shown below is a time lapse video displaying one of two pneumatic drills that we use to create the injection hole pattern. The drill is capable of drilling up to one lane mile per day. This equipment, known as the “gang drill”, is used for large projects where multiple lane miles of pavement are being lifted and stabilized.
CREWS IN ACTION
Shown below is a time lapse video of Nortex crews in action. In the project shown below, a general contractor was adding an additional third lane to the existing two lane eastbound/westbound road. However, the existing lanes had transverse faulting throughout the entire 3 mile stretch. The city did not want the faulted lanes adjacent to the new smooth lane, so Nortex was hired on to repair them. Using polyurethane foam injection in combination with polygrinding, we were able to greatly increase the ride quality of the existing lanes, extending the life of the pavement, and avoiding long periods of downtime.
LIFTING ROAD DIPS
When several concrete panels settle across all lanes, it forms a dip. Dips can be quite dangerous, especially when driven over at high speeds or when they are holding water, causing drivers to hydroplane. By injecting these dips with high-density polyurethane foam, these dips can be eliminated in just a matter of hours.
Pictured below is a dip that had formed in front of an entrance to a school campus. The dip had settled 6 inches and was becoming a safety hazard. Crews worked one lane at a time, setting up a string line so that the road would be lifted back up to the correct elevation. This project was completed 3 years ago, and since then, no further settlement has occurred.
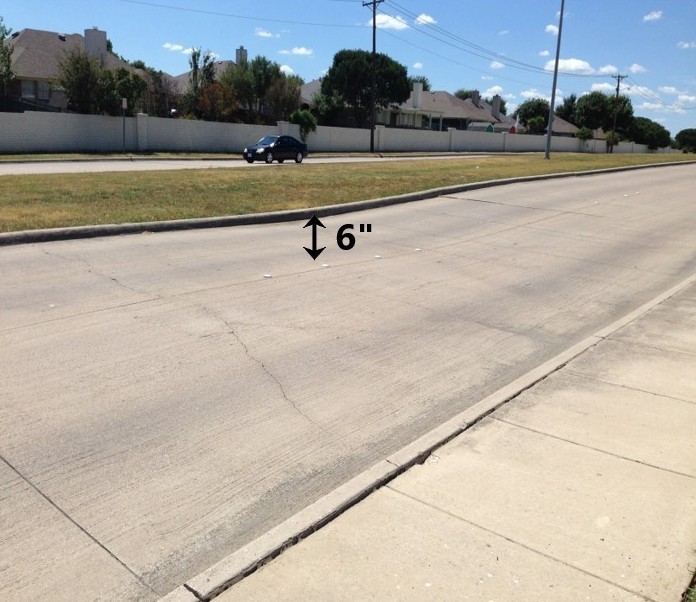

VOID FILL BENEATH ARTERIAL ROAD
The video below shows how our foam reacts as it is pumped into a large void beneath an arterial road. This road was built on top of an old landfill, which eventually lead to severe settlement and erosion of sub-grade soils beneath the concrete pavement.
JOINT MATCHING
The project below pictures a long concrete slab that had settled a couple inches. The settled slab was holding water and frustrating to drive over. Cutting out the concrete and replacing it would only temporarily fix the problem because the poorly compacted sub-grade soils would eventually allow the slab to settle again. As seen below, our crew injected high-density polyurethane foam, fixing the root of the problem. The crew easily lifted the slab back into place in only a few hours.
WEIGH STATION APPROACH SLAB
In the project below, a weigh station approach slab had settled approximately 5 inches. Using our high-density polyurethane foam, we were able to lift the slab back up to its proper elevation within a matter of hours.
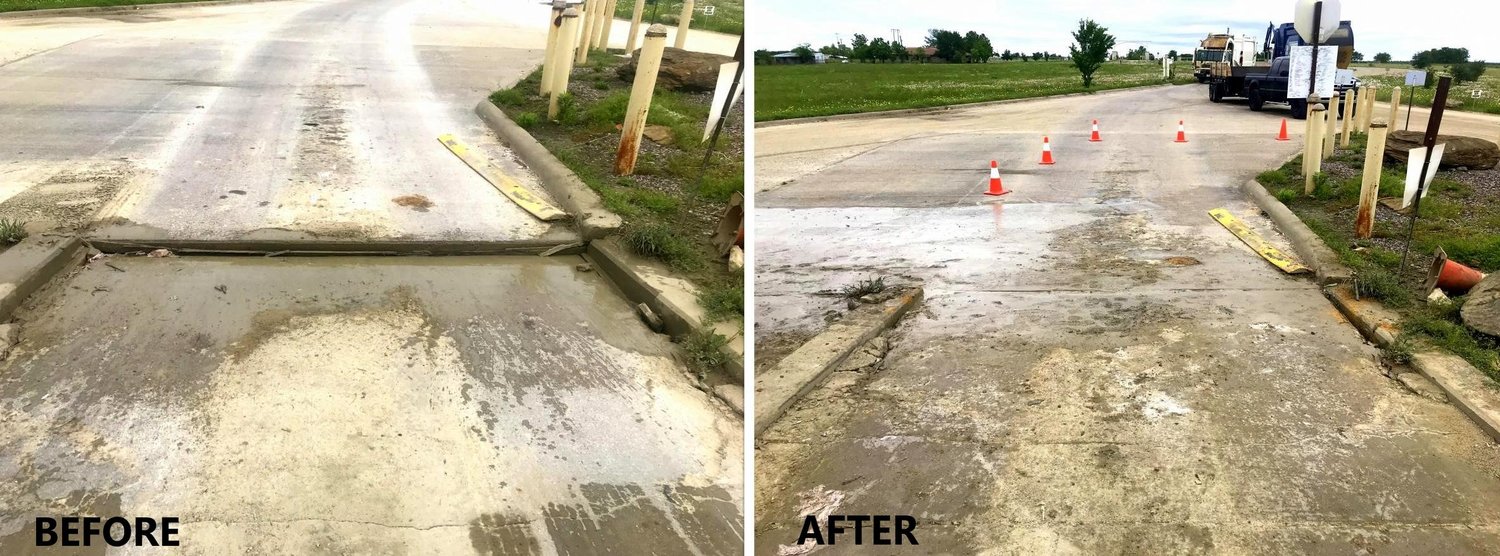
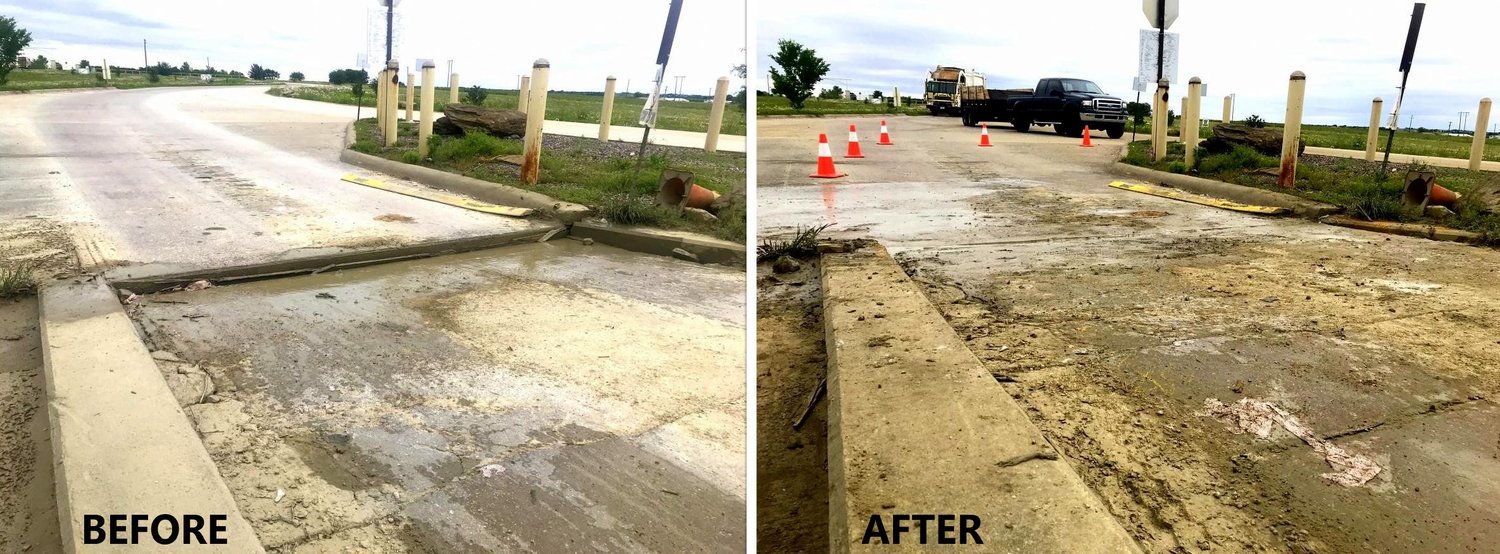